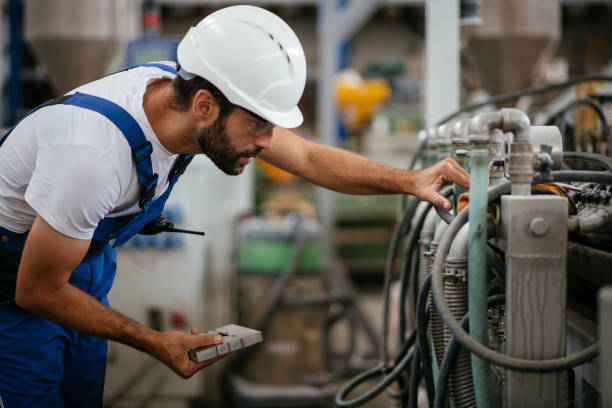
Equipment and plant servicing is the regular maintenance, testing, and repair of machines, tools, and mechanical systems used in industries such as construction, warehousing, and manufacturing. It keeps machines running properly, helps avoid sudden breakdowns, and keeps workers safe.
Businesses that rely on machines must make sure their equipment is working as it should. This means checking parts, cleaning systems, replacing worn items, and fixing faults before they become a bigger problem. When a machine stops working, it can stop the whole operation. That’s why regular servicing is so important.
In the UK, equipment and plant servicing is not just a good idea, it’s also required by law. Health and safety rules expect businesses to keep machinery in good working order. Ignoring these rules can lead to accidents, big fines, or loss of business.
Servicing should be done by trained professionals who understand each piece of equipment. It may include checking engine parts, testing controls, topping up fluids, tightening bolts, or replacing worn pieces. How often servicing is needed depends on the type of equipment and how much it’s used.
In this article, we will explain everything you need to know about equipment and plant servicing. We’ll cover how it works, why it matters, how often it should be done, and how it helps protect your business, workers, and profits.
Why Equipment And Plant Service Is A Must For Every Industry
Whether it’s a forklift, conveyor belt, generator, or digger, all machinery wears down over time. Equipment and plant servicing is what keeps these vital machines in working condition. If you run a business that depends on machinery, skipping regular servicing is risky. It puts your workers, your output, and your reputation at risk.
1. Keeps Operations Running Smoothly: Breakdowns can bring everything to a halt. If a key machine fails, your team may be stuck waiting for repairs, and work gets delayed. Servicing spots faults early, allowing small fixes before they turn into big problems. This means fewer stoppages and better use of time.
2. Prevents Expensive Repairs: Replacing major parts or an entire machine can cost thousands. But catching a worn belt or loose bolt early can save money. Regular servicing is far cheaper than emergency repairs. It also extends the life of your equipment, so you get more value out of your investment.
3. Improves Safety For Workers: Faulty machinery is a major cause of workplace accidents. Brakes can fail, parts can snap, and leaks can lead to slips or fires. Servicing includes safety checks, making sure that machines are safe to use. This protects your workers and helps you meet health and safety rules.
4. Meets Legal and Insurance Requirements: In the UK, many machines must be inspected under the Provision and Use of Work Equipment Regulations (PUWER). Failing to service equipment could mean your insurance becomes invalid or your business is fined. Keeping up with servicing shows you are taking your responsibilities seriously.
5. Maintains Good Business Image: Clients and partners notice when your operation is clean, safe, and efficient. If your machines are breaking down or making loud noises, it reflects poorly on your business. Serviced machines perform better and show you care about quality and safety.
No matter the industry, equipment and plant service process should be a regular part of your routine. It saves money, avoids downtime, and protects your staff. Whether your machinery is large or small, keeping it in top condition helps your business run better.
How Equipment And Plant Servicing Is Carried Out
Understanding how equipment and plant service is done can help you make better decisions for your business. Servicing is not just a quick check. It’s a full process designed to keep your machines safe, reliable, and working as they should. This process should always be carried out by trained professionals with the right skills and tools.
1. Initial Inspection
The first step is always a full check of the equipment. This involves looking at each part of the machine, checking for wear and tear, listening for odd noises, and spotting any early signs of damage. Engineers often use checklists to make sure nothing is missed.
2. Cleaning and Lubrication
Dirt, dust, and grease can build up inside and around moving parts. Cleaning these areas helps the equipment run smoother. Lubrication is also important. It stops parts from grinding against each other, reducing the chance of wear, heat, or failure.
3. Testing Key Systems
Servicing includes testing the machine’s working systems. For example, brakes, lights, pressure levels, controls, and alarms are all tested. In some cases, parts may need to be removed, tested separately, and then put back.
4. Replacing Worn Parts
If a part is damaged or likely to fail soon, it is replaced straight away. This could be anything from a belt or a filter to a battery or valve. Using quality replacement parts ensures the equipment stays reliable.
5. Reporting and Records
Once the work is done, a full report is written. This will include what was checked, what was replaced, any repairs made, and when the next service is due. These records are important for both safety checks and legal purposes.
6. Safety Sign-Off
After everything is done, the equipment is signed off as safe to use. This gives peace of mind to the operator and the business owner.
In short, equipment and plant services is a step-by-step process that checks, fixes, and improves your machinery. It’s more than just a wipe down or oil change. It keeps everything running right, so your business can carry on without problems.
What Happens When Equipment And Plant Servicing Is Ignored
Failing to carry out regular equipment and plant service process can lead to serious problems for any business. While it may seem like a way to save time or money, the long-term effects are usually far worse. Ignoring servicing creates safety risks, increases repair costs, reduces productivity, and damages your company’s reputation.
1. Sudden Breakdowns
Without servicing, machines are more likely to stop working without warning. When a key piece of equipment fails, operations slow down or stop altogether. This delay affects delivery schedules, customer satisfaction, employee performance, plus income.
2. Higher Repair Costs
Minor faults that go unnoticed often develop into larger issues. Replacing a simple part during servicing costs far less than replacing an entire machine or paying for emergency repairs. Waiting too long can also mean longer repair times, which adds to business disruption.
3. Safety Risks
Equipment that hasn’t been serviced may be unsafe to use. Loose parts, fluid leaks, poor brakes, or faulty wiring can result in workplace accidents. Staff injuries, legal claims, inspections, or insurance complications often follow when safety is ignored.
4. Legal Trouble
In the UK, regulations such as PUWER (Provision and Use of Work Equipment Regulations) require businesses to keep machinery in good working condition. If an incident occurs due to neglected servicing, your business could face investigations, fines, or temporary closure.
5. Poor Efficiency
Un-serviced machines usually use more energy, break down more often, or take longer to do their job. This slows down production, increases running costs, plus puts more pressure on staff to meet targets.
6. Shorter Equipment Lifespan
Without regular care, the useful life of a machine is greatly reduced. Worn parts create stress on the rest of the system, leading to further damage. Eventually, you may need to replace machines sooner than expected.
Avoiding these problems is simple: stick to a regular servicing schedule. Keeping up with equipment and plant servicing saves money, improves safety, boosts efficiency, and protects your business in the long run.
Who Needs Equipment And Plant Maintenance In The UK?
Equipment and plant service process is vital for any business that relies on machinery to operate. Whether it’s a small firm with a few tools or a large site with dozens of machines, regular servicing ensures safe, smooth, and legal operations. The need applies across a wide range of sectors in the UK.
1. Construction Firms
Construction sites use heavy machinery such as diggers, cranes, cement mixers, plus generators. These machines work in tough conditions with dust, mud, moisture, or constant movement. Without servicing, these factors can quickly wear out parts, cause leaks, or make the machine unsafe to use.
2. Warehouses and Distribution Centres
Forklifts, conveyors, packing machines, pallet trucks — these are often in constant use. Missed servicing can lead to breakdowns during busy periods, slower loading times, or health risks for operators using faulty equipment.
3. Manufacturing Facilities
Production lines depend on machines to work accurately without errors. A fault in one machine can stop an entire process. Servicing reduces downtime, ensures product quality, boosts output, plus avoids production loss.
4. Agriculture and Farming
Tractors, sprayers, harvesters, and irrigation systems all require regular checks. Working in the fields exposes equipment to rough ground, moisture, plus weather changes. Servicing helps farmers avoid breakdowns during planting or harvest season, which could impact their income.
5. Public Services and Councils
Local authorities use vehicles and machines for roadworks, waste collection, cleaning, or maintenance. Regular checks reduce the chance of mechanical failure during essential services or when working in public spaces.
6. Property Maintenance and Facilities Management
Businesses that manage large buildings or estates often use machinery for repairs, lifting, outdoor works, or internal transport. If these tools fail, it can disrupt services for tenants, staff, or customers.
Whether your machinery is used daily or occasionally, equipment and plant servicing helps ensure safety, improve reliability, lower long-term costs, plus keep your operation within legal standards. No matter the industry, if machines play a role in your business, servicing should never be ignored.
Let Us Help You Keep Your Equipment Safe And Running
Hiring experts for equipment and plant servicing is one of the smartest decisions I’ve seen businesses make. It’s not just about ticking off a task, it’s about protecting your staff, keeping your machines working properly, avoiding downtime, plus meeting safety standards. I’ve watched companies struggle because they left their machines unchecked for too long. I’ve also seen how quickly problems disappear once proper servicing is in place.
At Legacy GLM Group, we don’t believe in shortcuts. Our team inspects, maintains, plus repairs all types of machinery with care. Whether you manage a warehouse, building site, or public facility, we bring knowledge, reliability, plus quick turnaround times to every job. We handle the servicing, the reporting, plus the reminders, so you don’t have to worry about missing a date or falling behind on legal duties.
If you’re unsure when your last service took place, or if your machines are starting to show signs of wear, now is the time to act. Waiting often leads to higher repair costs or safety risks that could have been avoided.
Call Legacy GLM Group today on 02392 985 776 to arrange your equipment servicing. Let’s protect your business from breakdowns, keep your w